
In the fast-paced world of logistics and cargo, shipment delays can significantly impact customer satisfaction and business efficiency. Understanding how to avoid shipment delay is essential for any logistics provider. This article outlines key strategies and best practices to ensure timely deliveries and minimize disruptions.
Understanding Shipment Delay
What Causes Shipment Delays?
Several factors can contribute to shipment delays, including:
- Weather Conditions: Severe weather can disrupt transportation schedules.
- Customs Clearance: Delays in customs can occur due to incomplete documentation or regulatory issues.
- Transportation Issues: Mechanical failures, accidents, or traffic congestion can impede timely delivery.
- Supply Chain Disruptions: Shortages of materials or labor strikes can halt operations.
Impact of Shipment Delays
Shipment delays can lead to:
- Customer Dissatisfaction: Late deliveries can erode customer trust and loyalty.
- Increased Costs: Delays often result in additional costs such as storage fees or expedited shipping charges.
- Operational Inefficiencies: Delays disrupt the flow of goods, causing bottlenecks and inefficiencies in the supply chain.
Also Read : Choosing the right logistic it is not difficult, why ? Read this.
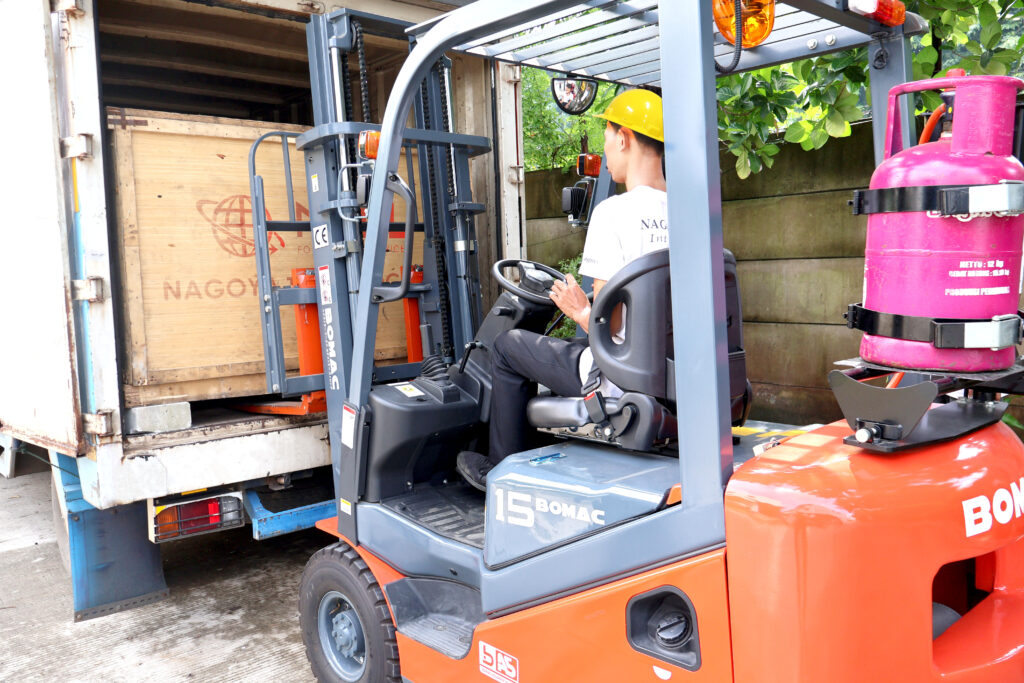
Strategies to Avoid Shipment Delays
1. Effective Planning and Scheduling
How to avoid shipment delay starts with meticulous planning and scheduling:
- Forecast Demand: Use historical data and market analysis to predict demand accurately.
- Plan Routes: Optimize routes to minimize travel time and avoid congested areas.
- Schedule Flexibility: Build flexibility into schedules to accommodate unforeseen delays.
2. Comprehensive Documentation
Incomplete or inaccurate documentation is a common cause of delays:
- Ensure Accuracy: Double-check all shipping documents for accuracy.
- Stay Updated: Keep up with changes in international shipping regulations and ensure compliance.
- Prepare in Advance: Prepare all necessary documentation well in advance of the shipping date.
3. Reliable Partnerships
Partnering with reliable service providers is crucial:
- Select Reputable Carriers: Choose carriers with a track record of on-time deliveries.
- Evaluate Performance: Regularly assess the performance of your partners and hold them accountable.
- Build Relationships: Foster strong relationships with carriers to ensure priority service during peak times.
4. Efficient Inventory Management
Effective inventory management helps prevent delays:
- Maintain Optimal Stock Levels: Keep sufficient stock to meet demand without overstocking.
- Use Technology: Implement inventory management software to track stock levels in real-time.
- Streamline Processes: Simplify and standardize inventory processes to reduce handling time.
5. Advanced Technology and Tracking
Leveraging technology can significantly reduce delays:
- Implement Tracking Systems: Use GPS and RFID tracking to monitor shipments in real-time.
- Automate Processes: Automate shipping processes to reduce manual errors and speed up operations.
- Data Analytics: Use data analytics to identify patterns and predict potential delays.
6. Responsive Customer Communication
Proactive communication with customers can mitigate the impact of delays:
- Provide Updates: Keep customers informed about the status of their shipments.
- Set Expectations: Clearly communicate delivery timelines and potential delays.
- Offer Solutions: Provide alternative solutions such as expedited shipping or refunds in case of delays.
7. Risk Management and Contingency Planning
Prepare for potential disruptions with a robust risk management plan:
- Identify Risks: Conduct a thorough risk assessment to identify potential sources of delay.
- Develop Contingency Plans: Have backup plans in place for various scenarios, such as alternative routes or carriers.
- Regular Reviews: Regularly review and update risk management plans to address new challenges.
Also Read : Want to export or import? Prepare your documents.
Case Studies: Successful Strategies in Action
Leveraging Technology for Timely Deliveries
Company A implemented advanced tracking systems and automated their shipping processes, resulting in a 30% reduction in shipment delays.
Building Strong Carrier Partnerships
Company B focused on building strong relationships with their carriers, ensuring priority service during peak seasons and reducing delays by 20%.
Conclusion How to Avoid Shipment Delay
Understanding how to avoid shipment delay is crucial for maintaining customer satisfaction and operational efficiency in logistics and cargo. By implementing effective planning, maintaining accurate documentation, partnering with reliable carriers, managing inventory efficiently, leveraging technology, communicating proactively with customers, and preparing for potential risks, businesses can significantly reduce the risk of shipment delays. These strategies not only enhance customer satisfaction but also contribute to the overall success and growth of the logistics operation.
- How to Avoid Shipment Delay in Logistics and CargoIn the fast-paced world of logistics and cargo, shipment delays can significantly impact customer satisfaction and business efficiency. Understanding how
- How Many Documents Do You Need for International Shipping?International shipping is a complex process that requires careful preparation and documentation. Proper documentation is crucial for ensuring that goods
- Choosing The Right Logistics Service, Read it Before DecidingChoosing the right logistics service is crucial to ensure your goods arrive safely, on time, and cost-efficiently. We have 9
- Choose Between FCL and LCL Shipping For Best ShippingChoose Between FCL and LCL Shipping – When it comes to International Shipping, businesses often face the decision of whether